Go offline with the Player FM app!
Episode 26 - Marc Bovet, BONE Structure
Manage episode 327006719 series 2523362
Listen to the episode
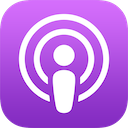
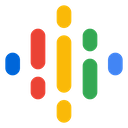

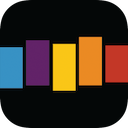
Prefab Review
Hi my name is Michael Frank and this is The Prefab Pod presented by Prefab Review where we interview leading people and companies in the prefab housing industry. Today, we're speaking with Marc Bovet of BONE Structure - a building system, I’m not actually sure if you consider yourself a prefab company, that's responsible for homes across the US and Canada. Marc, thanks for joining.
Marc Bovet - BONE Structure
Well thank you, Michael. It's a pleasure to be here.
Prefab Review
I guess to start, can you tell me a bit about your background and how you became involved in building homes?
BONE Structure
Yeah, well the short version of the story is that like many people out there who have initiated to build a brand new home, and back then I was part of the management at the world class company, Bombardier, and traveling quite a bit and my wife basically undertook the project. So she went out and we hired the very best architects and very best engineers and we laid out the plans and you know, we went through the whole sequence. And with the smallest details because I'm that type of individual and so is my wife, and sure enough when the time came, we went out there and got 5 builders to come in and look at the plans and come up with some quotes and timelines. Believe it or not, when all of those came back there was a delta from 5% to 72%, without having 2 of them close to each other. So back then, we asked the architect, “did you send the same set of plans to everybody because something is fundamentally wrong here or appears to be wrong?” So that's how this quest really started. It really got me fired up and I've been in the apparel industry most of my life. I was in the advertising business. I was a consultant for many small, medium and large companies and bombardier was one of them. And I was part of the management at Bombardier back then and we were implementing six sigma which was the world class recipe to make it right. And so what I did is I reviewed the whole thing and tagged it just as if it was a six sigma project which no one in his good common sense would do for a residential project. I mean people don't even go that far even for a skyscraper or an industrial complex. But this way I was satisfying myself and saying, “you know we'll get things out there. We will be ready. There will be no surprises and let's not fall into a trap of having late deliveries or having not double checked what we were ordering and finishes and so on.” So with all of that preparation and that eccentric craziness of a gantt charting exercise. With all the possible buffers of what a nordic climate could bring to you from an ice storm to a snowstorm to anything. We went along and finally decided to opt for and this is one of the most significant things to be remembered, we opted for someone that we trusted and at the end of the day it was none of the 5 forecomers that we had initially welcomed. So we went on with someone that had to drive fifty miles every single day. He was a GC and he had his own team. So the conditions were clear: finish all your job sites, finish all your contracts and the day that you will come here, you will be fully dedicated with your team on this job site. So he accepted the challenge which he probably regretted when I pulled out the gantt chart and then he said, "oh crap, what am I getting into here." But to a certain degree, we had sort of facilitated his job because he saw that we went into the extreme planning
Prefab Review
Yeah, yeah.
BONE Structure
And with the buffers and everything else making his life easier. All that being said, and I did mention buffers - we ended up, my wife and I, with four kids in a hotel room. So that got me thinking, if it was a hundred million dollar project, which it was not, trust me, how is it that Mr and Mrs Jones and our architectural firm and John the contractor and our sub-trades can make things happen with rigor and discipline? And keep in mind that is all orchestrated. So we started to do research and it became sort of a pet project at the beginning. So I had some research done personally. I did some research and I've put full people on it. And we've looked at everything and in the end anything that was prefab, modular, industrialized platforms concepts North America, Asia, you name it, we pretty much looked at it. In fact, we looked at thousands of patents even before getting into the game. And the more we were digging the more we realized that this was for good or worse a very artisanal industry which goes by, "well, we've always done it this way" and to a certain extent and to a certain extent with all due respect to some of the best prefabs out there, at the end of the day it's we've always done it this way, but you add on the prefab. So we really wanted to challenge all of this and take the knowledge of people that I've hired and put a team together and really create some sort of A team here where we would just pulverize and come up with a totally different mindset and look back, as far as in California per-s, the first home that was built in California was in 1800 or so. Take it or leave it, for the past two hundred years we've been doing the same old thing with about the same materials. It's just that because of manufacturing facilities, because of different processes, because of certain things nowadays, even facilities, capabilities and digital capacities that we have out there. The industry has reinvented itself and you've seen over the past twenty four months covid being just a sideline to this, seen some pretty incredible big companies which we won't name, that had humongous funding that were supposed to come and revitalize and reorganize and restructure the industry. If you look right now, what's happening in Australia and New Zealand and so on and so forth. So, at the end of the day the way we went about it is, "let's not look at what the industry's been doing but let's look at what human behavior needs and redefine what home is and redefine what the expectations are. What is the relationship between individuals be materials and availability of labor and so on so forth?" So you basically said it well in your introduction: we are and we are not prefab and this is where I personally always try to make sure that individuals who are having a conversation are set on the same definitions of a word or a sentence. For example, prefab in California is sort of cool. It's the fear of missing out. I want my ADU type of mindset. If you go into the northeast whether it's in Canada or the US, it has a connotation of a cheaper product. It's like, "oh you can't afford a real home." Okay I get it, and you're far past a trailer home. But it's prefab, so depending on where you are from east to West to North to South, we are very careful. And this is wh, yes we are much more understood as a building system with integrated technology. That's why we have our own proprietary technology. It's patented in 25 countries with 25 mindset rules, regulations, countries, languages, human species and different habits in mind which is a little bit wider than some restrictions imposed by what the typical quote prefab industry is limiting itself by default in terms of transportation or in terms of availability of cranes or whatever to manipulate those prefabs whether they are modules whether they are walls whether they are so and so. So we've looked at the whole spectrum of not just materials and or labor or manufacturing facility. But we've taken it and completely spinned it totally 360 with the end user in mined and the legacy of that dwelling with mother nature with its surroundings.
Prefab Review
Cool. So let's get into, that's an awesome backstory. So ah, let's get into some of the specifics of what makes a BONE home a BONE home. I mean obviously, I believe your homes all have steel frames. But do you think you can get into but I know you don't want to simplify you know this sort of thing, yeah what makes your home special? Do you think you can sort of give me a quick summary of the real distinguishing things about your homes versus maybe another home whether stick built or prefab or kit or whatever?
BONE Structure
Yeah, sure because that's the point there's so many offerings out there but there's some pretty good offerings out there and you know there's room for everybody. Let's put it this way. And we're very open-minded. I think we have a culture in our company which is based obviously on innovation and open mindedness that sometimes is surprising because I've had the pleasure to be a speaker at different conferences and sometimes we chit-chat with what could be seen as a competitor and I always tell them, "we're not competitors. We're trying to fulfill a need out there and we're all doing our very best and sure, we can even share some best practices because there's so much to be done to make it a better world. I know it sounds cliche but there's definitely so much to be done to make it better." So yes, at the end of the day, let me take you to one of my favorite analogies which basically underwrites the trademark of our product. The BONE Structure, I mean as we look at what Le coeur bosier, Frank llod Wright, Edison which I call the light bulb guy, even had his prefab system and there's a full drawer of those innovative ingenious people, architects engineers and everybody else. And what we understood as we looked at all these different possibilities, is that there's one concept out there that has basically passed the test of time: the ultimate test of time was design for the utmost best. Never reformatted, rethought structure, which is the human species BONE Structure. So Michael, my turn to ask you a question, how many bones do you have in your body?
Prefab Review
Yeah, I'm trying to avoid ah googling that. A lot. Hundreds.
BONE Structure
Okay, well let me whisper that answer to you. Surprisingly, even if we don't know each other, I know that you have 206 bones. Same for Mrs Jones the same for Mr Thompson and the same for the 8,000,000,000 people on this planet. So that's what I call integrated design because it's been around for a while and it hasn't changed. Case and point the bone structure was designed so that it survives the tests of time no matter what personality character you would want to dress it up with being architecture, interior design, so on and so forth. So the most important thing about a dwelling, about a home about a commercial building is the structure and it's thermal envelope so that it will sufese the test of time. Everything else is sort of, I don't want to banalize it, but flavor of the month, trend of the year, color of the day, and so on and so forth. So when you look at european architecture, when you look at the buildings, the homes that've been around, and if you had the chance to go to Rome or if you had the chance to travel the world you will see that those that have lasted time and time again, it's not only because of architecture. It's not only because of the personality and the character but there were some fundamentals that were defined at the very basic of the design. So the BONE Structure is different, yes because we use a material that is 100% recyclable. We are using a material that will be there in fifty, one hundred, hundred and fifty years but where we've pushed the exercise is that we've made it simple enough that it becomes an assembly on a job site. Not a modular positioning, not a crane exercise, not a wall exercise. It becomes a skeleton that gives the architects and the architects of this world and the interior designers of this world all the desired flexibility because of its engineering capacity. So for the workers on the job side it's assembled because everything clips one into the other that easy.
For the architects it gives them the flexibility of design and open spaces because we have just about no interior load bearing walls. The same goes for the interior designers, the same goes for the architects and so on and so forth and it enables us to have a living in symbiosis with what mother nature has to offer. Now mind you, sometimes in an urban living downtown San Francisco, you might not have that luxury of having the size of living with your neighbors. But then again, because it is an assembly of parts like a good old erector set, which was there before the lego toy set, it enables you to go and build an infill in one of those crooked streets in San Francisco with the feasibility, accessibility of workers basically clipping parts together so that they can create an environment that will fulfill today's needs and future generations needs because unfortunately, we the human species, have not understood and carefully looked at the history of home building where, even though some of the best practices out there will say yes this home is there forever, but guess what, as people are moving from one size of a home to another size of a home, or from one state to another state, or from one country to another country, and they're coming with their own culture and their own needs some people want two different kitchens. Some people want larger bedrooms. Some people want larger dining rooms. Some people don't want dining rooms. They want a family room. Well, guess what? How is it that these homes are not able to adapt to those new owners? And this is something that we at BONE Structure have been able to do because of our integrated design services being able to fulfill so either with outside architects or within our own professional architects inside because of the basic design of our industrial building system platform, we are able just like the human species, we are able to create 8,000,000,000 different propositions that can be come alive with architecture, with personality and character, with local materials so that we make a significant difference not only in creating beautiful home that live in symbiosis with their environment but also long lasting adaptable homes so that you can remove or add on walls, remove or add on windows, basically reconfigure the whole skeleton. Or should I say the outside shell to adapt to what the skeleton enables you to do so. That's part of what makes us unique, is that we're not just designing homes or having homes designed just to fulfill the needs of the individuals that command us to do it. But we also think fast forward into who else might inherit it because that's becoming the trend or should I say it will be forced onto American society. Because of the cost of owning a home while now like Europeans have been doing for the past century is that you will most probably as a responsible parent look at the possibility of leaving that home to your succession to your kids because they otherwise might not be able to afford a home for that matter.
Prefab Review
That makes sense. Yeah, home prices have certainly gone pricey in a lot of markets. Just to sort of get down to the specifics, so if I'm a consumer and I come to you and I call you to say, "hey, I love the homes I've seen on the site. I'd like to work with you. Do you think you can kind of run me through the process of what that means?" Yeah, to understand, you build the steel frame, you know, are you in this example at least, are you also the architect who hires the local builder? How does all this stuff work?
BONE Structure
It's very simple in the sense that we accompany you to make one of those 1,000 decisions you'll have to make in building your own custom home. Meaning that in the past fifteen years we're not using the language or the vocabulary that has become trendy in you know, local sourcing or life cycle or energy efficiency. This is not what bone structure is all about. So as Michael Frank comes and joins us or asks us to accompany him, we will go with a go left, go right, go left, go right, go straight conversation depending on where you are.
Prefab Review
Yeah, sure.
BONE Structure
And how you want to make things happen, so we accompany you in the process. So let's say for one you say, you know, "my house just burned down in Sonoma and I don't know if I want to rebuild there. I'm really scared, they told us it was a 100 year thing and it's been coming back every year, so I guess I'm 300 years older now and so on and so forth." So obviously we have a better proposition because in terms of fire rebuilds we have the utmost technology to prevent that unfortunate or the result of that circumstance, so we will tell you, "listen, we have an inside architectural service. We can design for you." Well, Michael you say, "yeah, but you know what? I have my friend as an architect, and you know he's been prying me to to get his services and so on and so forth. I Wish that we could use the services." No problem. Let's put him around the table. The thing here is that it's a collaboration. It's getting everybody possible around the table that can make this dream come true. So either we go with your outside architect which then,if you go with us it's very simple, what we'll do is that we'll do a design contract service. Human species wants to go one step forward and one step backward. We don't want to corner a client into a service. So if you're not buying a house from us, you're buying first a professional service of design. We will design it. Then we'll go into an immaterial contract which if you desire to go that way which 95% of people do with us because they entrust us with the service and we help them figure out if BONE Structure is the best proposition for them. Before we start working with them, sometimes we do refer them to other prefab or modular or other traditional builders. We're not shy to do that. We want to make sure that it's not a customer relationship we have. It's a client relationship that we develop. And a client for us is a lifetime experience. It's not a transactional thing. So we sit down with Michael Frank and a convenient partner and we set up and review the wish list from there and we make sense of that wish list and the budget because in this industry whether it's prefab whether it's modular whether it's traditional building, that is the elephant in the room. Budget - does it align with what the market can suffice today and that is are we good to make sure we start with the right interpretation of what these variables are then we get our design team to design it. We're very much into digital design. We've been at it and we've been at the forefront of it for the past twelve years, so when I hear people telling me that, "oh yes, now we've got bim." Well guess what, we've been for at least 9 years now. We've always been on the forefront of making sure that in terms of digital technology we are on the edge. So we designed a home obviously with the implementation in mined with everything that mother nature has to offer with what that lot has to offer and so on and so forth. We present that to the clients and we make as many iterations as we need to. Fortunately, our team is talented. Normally we are able to guide the client to make the right decisions as we go and are able to limit those iterations before they get crazy or we get crazy. So we've learned a lot about that and we're proud to say that we have a very seamless process. So then you have the 3D full version I'll drive you through the home if you want you can put the helmet on and you can visualize your home. You can live it and if you want to buy that version and live with that one, that's okay with me. But we'd prefer you go through and go with the real home. And so then we'll be doing the estimate of what that thermal envelope is going to cost you. That's the pure proprietary system. It's the BONE Structure. It's the thermal envelope. It's the insulation. It's the doors and windows and that's basically what makes us totally different. Before you go into the kitchen counter, think of the conversation or plank floors or whatever outside finishes you want because that is whatever intentions are and you know as we say, everybody has some opinion about home decoration. But that is the most important thing because that is what will make you comfortable. This is where your home becomes a healthy environment, this is where it becomes durable, efficient, adaptable and so on and so forth. And then we go into let's look out there if we have not, have I identified them before which normally we did, we will present you to local builders that we have relationships with. If we don't, we will wit Michael Frank with the potential client look at what the community has to offer as the best builder out there that aligns with the philosophy that the client and BONE Structure have already figured out because a client that comes to BONE Structure has looked at different options and has realized as they were doing their due diligence that they were buying into a premium product. They were buying into what is the best to be offered out there. They know what they're getting into. Because it's simple to understand and it's logical and you know, sometimes one of the remarks we get from our potential clients that have just discovered us is why is it that everybody doesn't build this way? It's so obvious and I always like to say that our best clients are not the ones that know what they want. Because everybody comes in with a wish list. Anyone is and it will not be our best clients. They are the ones that know what they don't want. And you know what, I have yet to come to someone that wants to build a house that hasn't heard stories. Whether that's their own stories that they live through or stories they've heard from elsewhere, the whole project became a nightmare at one point or another. Either because of cost issues which in these days, it's a much more relevant issue and today it's exponential but because of delivery issues, because of sourcing issues, because of labor issues and so on. We're very different at BONE Structure we are still able to control the processes because it is part of it. Integrated design proposition, where the process is at the core of what we do, and that's what some of the big names have tried to do. Coming out from the cell phone industry or this industry, there's a lot of people coming from different trades: trying to bring in the outside processes. Well we've understood over the years and trust me, we've done our hits and misses too. We've done our trials and errors. Well, we've come to realize that the construction industry, the residential construction industry is a local market. I don't care how national your company is, at the end of the day it's a local market and this is where we at BONE Structure have worked with a 182 municipalities and townships so far in the US and in Canada. So we know how to deal with these groups and these municipalities, and our technology is accepted proven and tested and easy to understand because of all of its benefits. So we will choose a local builder with our client with Michael. We'll say, "Michael, this is the builder we would like you to meet. Or we will meet your builder with you and we figure out is this the best proposition." Because at the end of the day, what BONE Structure is really good at, and don't get me wrong, we're not picture perfect, my wife is perfect, but the rest of us are trying very hard, but the end game here is to mitigate the risk and this is what this industry is trying left, right, and center. Everybody's trying to come up with some different options. And from the 20 propositions that you have, and I congratulate you with your prefab podcast and the different interviews you've had with with the industry leaders and they all have good propositions. At the end of the day, everybody's trying to beat nature. They're trying to beat the process out of the human nature. We've looked at it from the human nature and adapted the process to help it out. So it's like the labor shortage in California seven years ago. The national homebuilders association has been, and don't quote me on the seven years, it may be 6 or 7 or 8 we should look at my files, but they said that 27% of builders could not find skilled carpenters. Same review two years ago that was before covid now imagine I should have to check it up, I think it was up to 85% of builders cannot find skilled carpenters. So, it's a major issue out there. This is why it's giving the prefab industry an edge but at the same time, the prefab industry has the same dilemma now they can't find labor to work in their manufacturing plants so they're trying to go industry 4.0 and push the envelope there, but that's capital intensive, as one of the companies you've mentioned. And again, you're trying to beat the process out of human nature. And what we're trying to do is to solve the issues and do it the opposite way. So we present you to the builders we have builders. We make the whole equation. We get the variables out of the equation to make it financially sound and to match your budget and match the timing and the planning that is necessary to realize your project.
Prefab Review
So are you doing the procurement even though obviously you're doing the procurement of the framing stuff and it sounds like the windows, but of the non-shell stuff?
BONE Structure
No, the non-shell stuff is that we will partner up with the builder and the client. But the builder, the local builder, which normally has his local resources and so on and so forth. We feel, and sure we're worthy, don't get me wrong, in a business sense we're leaving a lot of money behind, but we've understood that we need to do what we do best and we need to get the client's objective fulfilled and to do that, the best proposition is to be able to have everyone contribute with what they have in their toolbox. So that local builder has the ins and outs of what he can source and how and when. He's got his buddies and you can get those local materials and and so on and so forth and it's better for the planet, etc, etc. So tested and proven from Whistler, B.C. with enormous snow loads to Sonoma Valley to Hawaii, we've built in the Nordic climates and the eastern parts of Canada. We've realized that to respect some sort of a timeline to build a custom home that has a thousand decisions and idiosyncrasies and everybody has their own version of everything and anything. We monitor it but we give a lot to the local market.
Prefab Review
That makes sense. So in terms of, let's use this Sonoma example because it's fairly flat which is one variable we can take out for the purpose of this example. One of the questions we constantly get from people and I know it's not always the easiest for answers around general cost, let's assume in this example, and by the way it's March 23, 2022, so if there's a a steel shortage tomorrow, more than there already is, you know that's not taken into account, but let's assume that you're building I don't know, a 2,500 square foot or 3,000 square foot house in Sonoma on a flattish piece of land. You know it's to your very high standards but like you know, not insane relative to a normal home you build. What would we be looking at from a cost standpoint and I think a lot of times the way that is helpful to listeners to break this down is sort of like what is the cost of your services from a soft cost and from a hard cost standpoint and then you know whether it's a range or specific costs on the rest of the house.
BONE Structure
Michael, I'm so glad you asked this question. I'm sure that out of the 22 or 25 podcasts you've done, this is the question that people push back on. Let me give you my no-nonsense about that and this is one thing I have looked at the industry in the past and I've always come up with the same conclusion. Here's the question - how much does your car cost per wheel? So whether you have a tesla whether you have a BMW an Audi or whatever, you go into a showroom or if you go on any those of those websites and you go and ask how much does it cost per wheel? It would be an irrelevant comparison to what this industry has imposed as an index of cost which is the dollars per square foot which, if you want my no-nonsense about it and even if you don't want it, it doesn't make any logical sense but hey we've always done it this way. The reason is that if you can just imagine with me here and picture this, you have your beautiful lot. You've got this view of the grape vines and so on and so forth and we design a home and sure enough you want mother nature. You want the whole view. You want the whole spectrum. You want those beautiful openings and windows and so we design an eighteen feet ceiling on this beautiful, what you've described 2,300 or let's say 3,000 square foot home. Okay, but then I could show you something just as nice with a twelve feet ceiling
Prefab Review
Right. A lot less glass.
BONE Structure
Not just less glass. That's 30% less structure. 30% less insulation. So the dollars per square foot do not account for volume entry. It does not account for that. So to prove my point, I will come back to my own frustration when I initiated to build a house 20 years ago. It was already more than that where five builders came back to me with a delta of 72% or 77%. So what I'm telling you is, I would dare you Michael to take one design and get its cost by every prefab company and every traditional builder you can get your hands on. And I will guarantee and I will have put money down on the bet that with the same specs and the same details you will not get 2 prices identical.
Prefab Review
Yeah, I mean mean to be clear we don't usually do this with clients all the time but for what I'm describing for example, let's flip literally. Say you know.
BONE Structure
But I know what your question is. Its give me an indication where your proposition is positioned in the marketplace. So we're definitely a premium product. There's no hiding behind that because you know of the glazing, people come to us because of our architectural design because of our large glazing and so on and so forth. So we're definitely a premium product and in the bay area, I mean right now, you can go Bingo and
Prefab Review
Right, for $500 or $600 a square foot would be probably.
BONE Structure
But then again, BONE Structure technology in its terminal envelope is in the vicinity of 30% of your whole budget. So the big responsibility falls on that 70% of oh geez I saw this new flooring or jeez, I saw this new bathub. It's on that bathub is now only 15 grand versus the nice 5,000 grand bath tub we had planned you see where I'm going. And that's what human nature is all about. So that's what I'm telling you. Where we differ is we accompany as best as we can our clients because it's a long-term relationship not only with them but with our own common baby which is the BONE Structure home they're building. And we know for granted that there's a fair chance that in give or take 70 years from now, that would mean that our clients are in their thirtys and they will have a life expectancy of over one hundred so it's safe to say that 70 years from now there will be new occupants to this home and they will definitely want to change the cosmetics and the opening positions and the inside walls and so on and so forth and for that I must say there's very few if just about no propositions out there. It's definitely very difficult with traditional building and even also a little bit cumbersome with what is defined as pure prefab or modular. So I think that's one of our biggest significant advantages.
Prefab Review
That makes sense.
BONE Structure
And then the price point. Yes, we are a premium product but at least one thing needs to be said and we've heard it from our clients and even the ones that were, "oh, geez that's more expensive," but you know 3, 4, 5 years down the road when we survey them, they will tell you it was worth every penny. Even more so if their neighbors went through a flood or a fire or some other mother nature catastrophe because one example I've had very recently from a client, the whole municipality was flooded. So everybody out there that had some sort of a traditional framing whether it was prefab modular or traditional framing, one common denominator - most of them needless to say, that you've got mildew. You've got something going bad and I don't care what they're trying to sell you to get rid of that, it will not because that's what mother nature has imposed in terms of characteristics to wood. It will just suck up anything. With a BONE Structure, what our clients did, they just tore out the whole basement, they hosed down, literally hosed down and rebuilt. They were up and running in thirty days as their neighbors are still playing with claims with the insurance companies and trying to figure out how to get out of that mess.
Prefab Review
That's great. I had one or two questions about your product before we jump into our fire round. I guess one is that you mentioned cranes whether you need them or don't need them for your product; is that something that's necessary? Just because I honestly in Taho or Marin or you know parts of New York, like one of the places we have clients or people who we have conversations with all the time, have issues with just, "hey, I want to put this modular box here and I can't I can't get it down the road or I can't get the crane down the road." Is that something where there's more flexibility with your product.
BONE Structure
Absolutely, it's one of our biggest and I'm not saying we will not use some sort of a boom truck or something like that if need be, but the whole thinking behind it is that you should be able to assemble a BONE Structure system without out any of those materials or any of those. And one thing you didn't mention which is unfortunate as we're all on the same planet and all the echo and movement is making more impact. It seems to try to make more impact in any form when you need to plant or bring in a crane. It's not only to get it there, it's just that they'll have to cut pretty much everything that's on your land in terms of trees to swing that module in place, with all due respect. We've built, I remember that we've built a house and I don't care if you've got a satellite but we've built a house about two miles into a wooded country area that no one in his own right mind would've thought even existed there because even if you would be able to go through the hunt and try to find it, it is so well camouflaged within the woods because we just about cut only the trees that were needed to get the structure assembled meaning the footprint, everything else we left there. So I don't know of any other technology that could have made that happen per se.
Prefab Review
That's great, and the one other thing that I assume is also an advantage but we sort of counsel people when they're thinking about kind of kits and other systems versus modular, all the time. I assume your homes are probably financeable with kind of normal construction loans versus modular specific ones because the draw schedule is different, right?
BONE Structure
Sure, absolutely. And not only that, you know, depending on the financial institution and so on, we've had some pushbacks like any other modular or prefab company out there in the past. But once we get to talk to them and get them to realize what the product is and the logic and the sequence of it and so on and so forth, very rarely over the years have we hit a hard no. But it's normal. You've got to sit in the chair of that person and in one of those institutions or financial institutions that are basically just filling out a form and they have to click on that yes or no, and they just don't know how to answer it and you help them and guide them and help that client go through that conversation. And like I said, we're very agile at making that happen. And back to your building flexibility, we've done quite a bit of infills.
Prefab Review
Awesome.
BONE Structure
Um, so like I said if you imagine doing an infill in the bay area or in downtown Vancouver or downtown Toronto, it's not only that you cannot get big equipment there, it's just that you don't have room to park the damn equipment there. So it's it's more of bring your pieces this morning and assemble those and this is where we are the champions and in that matter even compared to traditional wood framing because even traditional wood framing will have some sort of an issue because they'll deliver bundles They won't deliver parts. If you see where I'm going.
Prefab Review
And it'll be a longer build process probably. Okay, so this has been awesome to get a bit more of a sense of your company, of your story. If it's okay, I was hoping we try to give everyone a quick fire round and get to kind of general issues with the building process. I guess so we've actually heard this a number of times when we've been helping people in Hawaii, "oh, BONE Sructures has done a couple projects over there." Can you tell me a little bit about building in Hawaii?
BONE Structure
We've done one project there. We did it because it was one of our clients and they were willing to go along and we were willing to go along with them. We're more concentrated and we're very focused on our dedicated markets: California obviously being one, now we're moving into Lake Taho, we're very much into Vermont, we're into New York state, and obviously we're definitely into British Columbia, and Canada, and Ontario, Toronto, and a little bit into the eastern parts in Quebec. But California is one of our biggest markets. This is where we're very dedicated because we're natural for it. We're natural for it whether it's for fire rebuild because of all the advantages we offer that. Whether it's because of energy efficiency, where you know we've been net-zero before they've been talking about net-zero. For us, it's a normal part of energy efficiency. It's not just another checkbox on our our wish list. We are in those markets also because clients like I said, there's more and more clients in California that know what they don't want than what they want. So we don't have to educate a client about energy efficiency and eco-friendly and all of that in California for all the good reasons and I don't have to lecture you on that at the same time. They definitely see the value proposition.
And they don't care how much money you have, a dollar spent into a home you want to make sure you get that value and it's not just about materials. It's to make sure that it's a healthy environment. It's adaptable and so on and so forth. So this is where the whole equation makes it the better proposition.
Prefab Review
Next question. I know I've talked to a few people who I believe are developers who have built with you. We work with work with a lot of developers. Do you talk about how, if at all, that's different from a process standpoint?
BONE Structure
For them, we're always you know, at one point, just to give you a little bit of background and show you how we're always looking for better ways of doing things, we at one point had offered only our products to our channel of selected builders. But at the same time we're shooting ourselves in the foot because we had so much demand and so many builders were basically wanting to come to work with this new technology and so we're very open minded. For the past five years, we've opened up the technology and we've basically aligned our processes to accompany those builders and their teams with the product. But again the product per se, the technology is helping those builders make a better business. What the builders are foreseeing right now is they have dedicated workers with them and sure enough because of covid or because John is now so capable that he bought his own pickup truck and he's now able to have his own clients. So builders, unfortunately the top builders out there, that are making the best homes, have the same labor issue as anyone out there. So with a technology that basically has the process built-in means that they can bring on someone to the team show them that this is a c bar from BONE Structure. Look, it goes here. Clip, clip, clip, you've got a thousand to do this morning Bob, go. And trust me these individuals coming onto our job sites get very excited because at the end of the day at the end of 1, 2, 3, 4 days they see what they've been working with and these immediate results. And they do not have to redo and that is one of the most underlying hidden costs from a builder's spreadsheet is the re-due line. This door was supposed to be here. We've redone it. We spent another 3 hours of carpentry. We had to bring in some more material. Let's remove this. Let's put this back. Because of the human nature of the clients, because of the human nature of the laborers, because people don't look at or read plans. That's human nature. So again, because of our integrated technology, integrated design into our technology, builders are facing labor shortages and with a technology like ours they do not need specific taining. They only need to line up holes with a bar and clip it. Even the logic about all of our hardware. We almost have only one screw available for the whole system. Not one, but almost 90% of the screws on that job site is the same screw. I dare you to go on a traditional job site and you'll see that you'll trip over boxes of different screws, different attachments, caulking tubes, and so on and so forth. The same goes with some other technology out there. So we're here again. We've turned the process around from human nature to technology. Not the technology imposing on human nature. As you are one of the consultants out there, I urge you to open up and broadcast that a BONE Structure is open to business with builders. Let's bring in their clients. Let's bring in their resources and let's let us help them give them the bones so they can do what they very do best: do the finishes and so on and so forth. Because the dilemma they have is that with a traditional construction, and you know this, they are as good as their last project. This new project is a totally new prototype for them, in traditional construction, every single home, even if it's a replicate becomes a new prototype with all its hidden costs and myths and hits and misses and labor shortages and not to say materials because I mean quality of the materials we're receiving in terms of the wood industry right now, man I wouldn't want to be there. I wouldn't want to be there. I mean I was talking to a builder who told me that the last job 40% of the structural wood he received be had to turn back which that's just diffifult. So it's all about predictability and where we help out the builders is to help them have their timelines more predictable and that is the biggest variable in the dollar equation right now. For a client or for an architect or for a builder or for a consultant like yourself is that no one has the crystal ball right now to fix a cost because of unpredictability on every front. We at BONE Structure mitigate the risk because we have a predictable system that enables us to assemble and then fill up with the cosmetics. Architecture design into a design and finishes and so on and so forth with what's available in a local market.
Prefab Review
That's great Mark. Thank you so much for being willing to join us today. It's been really great learning about your journey and learning about BONE Structure for everyone listening, if you'd like to learn more you can visit BONE Structure at bonestructure.ca and to learn more.
BONE Structure
That's capital BONE capital s for Structure BONEstructure.ca and I thank you Michael and I look forward to meeting you in person. Because you do have 206 bones and we someday will come back to shake hands. I guess someday, somehow and that will be fun. Yeah this version of covid you know.
Prefab Review
Yeah, it would be great. Yeah, as as we start to come out of Covid seems like is happening. Alright, thanks again. Mark this was great talking to you and we'll hopefully talk again soon. Thanks
BONE Structure
Thanks
Get Our Guide to Buying a Prefab House
Learn how to buy land, select the best house plan, get financing, calculate investment ROI, and more. Save hundreds of hours of research.
We respect your privacy.
Thank you! The guide will be emailed to you soon.
If you want even more support with your project, then signup for Prefab Concierge - our free service where you are paired with a member of our staff who provides you 1:1 support with your potential project -> Learn More
39 episodes
Manage episode 327006719 series 2523362
Listen to the episode
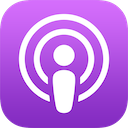
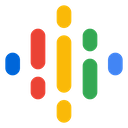

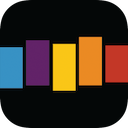
Prefab Review
Hi my name is Michael Frank and this is The Prefab Pod presented by Prefab Review where we interview leading people and companies in the prefab housing industry. Today, we're speaking with Marc Bovet of BONE Structure - a building system, I’m not actually sure if you consider yourself a prefab company, that's responsible for homes across the US and Canada. Marc, thanks for joining.
Marc Bovet - BONE Structure
Well thank you, Michael. It's a pleasure to be here.
Prefab Review
I guess to start, can you tell me a bit about your background and how you became involved in building homes?
BONE Structure
Yeah, well the short version of the story is that like many people out there who have initiated to build a brand new home, and back then I was part of the management at the world class company, Bombardier, and traveling quite a bit and my wife basically undertook the project. So she went out and we hired the very best architects and very best engineers and we laid out the plans and you know, we went through the whole sequence. And with the smallest details because I'm that type of individual and so is my wife, and sure enough when the time came, we went out there and got 5 builders to come in and look at the plans and come up with some quotes and timelines. Believe it or not, when all of those came back there was a delta from 5% to 72%, without having 2 of them close to each other. So back then, we asked the architect, “did you send the same set of plans to everybody because something is fundamentally wrong here or appears to be wrong?” So that's how this quest really started. It really got me fired up and I've been in the apparel industry most of my life. I was in the advertising business. I was a consultant for many small, medium and large companies and bombardier was one of them. And I was part of the management at Bombardier back then and we were implementing six sigma which was the world class recipe to make it right. And so what I did is I reviewed the whole thing and tagged it just as if it was a six sigma project which no one in his good common sense would do for a residential project. I mean people don't even go that far even for a skyscraper or an industrial complex. But this way I was satisfying myself and saying, “you know we'll get things out there. We will be ready. There will be no surprises and let's not fall into a trap of having late deliveries or having not double checked what we were ordering and finishes and so on.” So with all of that preparation and that eccentric craziness of a gantt charting exercise. With all the possible buffers of what a nordic climate could bring to you from an ice storm to a snowstorm to anything. We went along and finally decided to opt for and this is one of the most significant things to be remembered, we opted for someone that we trusted and at the end of the day it was none of the 5 forecomers that we had initially welcomed. So we went on with someone that had to drive fifty miles every single day. He was a GC and he had his own team. So the conditions were clear: finish all your job sites, finish all your contracts and the day that you will come here, you will be fully dedicated with your team on this job site. So he accepted the challenge which he probably regretted when I pulled out the gantt chart and then he said, "oh crap, what am I getting into here." But to a certain degree, we had sort of facilitated his job because he saw that we went into the extreme planning
Prefab Review
Yeah, yeah.
BONE Structure
And with the buffers and everything else making his life easier. All that being said, and I did mention buffers - we ended up, my wife and I, with four kids in a hotel room. So that got me thinking, if it was a hundred million dollar project, which it was not, trust me, how is it that Mr and Mrs Jones and our architectural firm and John the contractor and our sub-trades can make things happen with rigor and discipline? And keep in mind that is all orchestrated. So we started to do research and it became sort of a pet project at the beginning. So I had some research done personally. I did some research and I've put full people on it. And we've looked at everything and in the end anything that was prefab, modular, industrialized platforms concepts North America, Asia, you name it, we pretty much looked at it. In fact, we looked at thousands of patents even before getting into the game. And the more we were digging the more we realized that this was for good or worse a very artisanal industry which goes by, "well, we've always done it this way" and to a certain extent and to a certain extent with all due respect to some of the best prefabs out there, at the end of the day it's we've always done it this way, but you add on the prefab. So we really wanted to challenge all of this and take the knowledge of people that I've hired and put a team together and really create some sort of A team here where we would just pulverize and come up with a totally different mindset and look back, as far as in California per-s, the first home that was built in California was in 1800 or so. Take it or leave it, for the past two hundred years we've been doing the same old thing with about the same materials. It's just that because of manufacturing facilities, because of different processes, because of certain things nowadays, even facilities, capabilities and digital capacities that we have out there. The industry has reinvented itself and you've seen over the past twenty four months covid being just a sideline to this, seen some pretty incredible big companies which we won't name, that had humongous funding that were supposed to come and revitalize and reorganize and restructure the industry. If you look right now, what's happening in Australia and New Zealand and so on and so forth. So, at the end of the day the way we went about it is, "let's not look at what the industry's been doing but let's look at what human behavior needs and redefine what home is and redefine what the expectations are. What is the relationship between individuals be materials and availability of labor and so on so forth?" So you basically said it well in your introduction: we are and we are not prefab and this is where I personally always try to make sure that individuals who are having a conversation are set on the same definitions of a word or a sentence. For example, prefab in California is sort of cool. It's the fear of missing out. I want my ADU type of mindset. If you go into the northeast whether it's in Canada or the US, it has a connotation of a cheaper product. It's like, "oh you can't afford a real home." Okay I get it, and you're far past a trailer home. But it's prefab, so depending on where you are from east to West to North to South, we are very careful. And this is wh, yes we are much more understood as a building system with integrated technology. That's why we have our own proprietary technology. It's patented in 25 countries with 25 mindset rules, regulations, countries, languages, human species and different habits in mind which is a little bit wider than some restrictions imposed by what the typical quote prefab industry is limiting itself by default in terms of transportation or in terms of availability of cranes or whatever to manipulate those prefabs whether they are modules whether they are walls whether they are so and so. So we've looked at the whole spectrum of not just materials and or labor or manufacturing facility. But we've taken it and completely spinned it totally 360 with the end user in mined and the legacy of that dwelling with mother nature with its surroundings.
Prefab Review
Cool. So let's get into, that's an awesome backstory. So ah, let's get into some of the specifics of what makes a BONE home a BONE home. I mean obviously, I believe your homes all have steel frames. But do you think you can get into but I know you don't want to simplify you know this sort of thing, yeah what makes your home special? Do you think you can sort of give me a quick summary of the real distinguishing things about your homes versus maybe another home whether stick built or prefab or kit or whatever?
BONE Structure
Yeah, sure because that's the point there's so many offerings out there but there's some pretty good offerings out there and you know there's room for everybody. Let's put it this way. And we're very open-minded. I think we have a culture in our company which is based obviously on innovation and open mindedness that sometimes is surprising because I've had the pleasure to be a speaker at different conferences and sometimes we chit-chat with what could be seen as a competitor and I always tell them, "we're not competitors. We're trying to fulfill a need out there and we're all doing our very best and sure, we can even share some best practices because there's so much to be done to make it a better world. I know it sounds cliche but there's definitely so much to be done to make it better." So yes, at the end of the day, let me take you to one of my favorite analogies which basically underwrites the trademark of our product. The BONE Structure, I mean as we look at what Le coeur bosier, Frank llod Wright, Edison which I call the light bulb guy, even had his prefab system and there's a full drawer of those innovative ingenious people, architects engineers and everybody else. And what we understood as we looked at all these different possibilities, is that there's one concept out there that has basically passed the test of time: the ultimate test of time was design for the utmost best. Never reformatted, rethought structure, which is the human species BONE Structure. So Michael, my turn to ask you a question, how many bones do you have in your body?
Prefab Review
Yeah, I'm trying to avoid ah googling that. A lot. Hundreds.
BONE Structure
Okay, well let me whisper that answer to you. Surprisingly, even if we don't know each other, I know that you have 206 bones. Same for Mrs Jones the same for Mr Thompson and the same for the 8,000,000,000 people on this planet. So that's what I call integrated design because it's been around for a while and it hasn't changed. Case and point the bone structure was designed so that it survives the tests of time no matter what personality character you would want to dress it up with being architecture, interior design, so on and so forth. So the most important thing about a dwelling, about a home about a commercial building is the structure and it's thermal envelope so that it will sufese the test of time. Everything else is sort of, I don't want to banalize it, but flavor of the month, trend of the year, color of the day, and so on and so forth. So when you look at european architecture, when you look at the buildings, the homes that've been around, and if you had the chance to go to Rome or if you had the chance to travel the world you will see that those that have lasted time and time again, it's not only because of architecture. It's not only because of the personality and the character but there were some fundamentals that were defined at the very basic of the design. So the BONE Structure is different, yes because we use a material that is 100% recyclable. We are using a material that will be there in fifty, one hundred, hundred and fifty years but where we've pushed the exercise is that we've made it simple enough that it becomes an assembly on a job site. Not a modular positioning, not a crane exercise, not a wall exercise. It becomes a skeleton that gives the architects and the architects of this world and the interior designers of this world all the desired flexibility because of its engineering capacity. So for the workers on the job side it's assembled because everything clips one into the other that easy.
For the architects it gives them the flexibility of design and open spaces because we have just about no interior load bearing walls. The same goes for the interior designers, the same goes for the architects and so on and so forth and it enables us to have a living in symbiosis with what mother nature has to offer. Now mind you, sometimes in an urban living downtown San Francisco, you might not have that luxury of having the size of living with your neighbors. But then again, because it is an assembly of parts like a good old erector set, which was there before the lego toy set, it enables you to go and build an infill in one of those crooked streets in San Francisco with the feasibility, accessibility of workers basically clipping parts together so that they can create an environment that will fulfill today's needs and future generations needs because unfortunately, we the human species, have not understood and carefully looked at the history of home building where, even though some of the best practices out there will say yes this home is there forever, but guess what, as people are moving from one size of a home to another size of a home, or from one state to another state, or from one country to another country, and they're coming with their own culture and their own needs some people want two different kitchens. Some people want larger bedrooms. Some people want larger dining rooms. Some people don't want dining rooms. They want a family room. Well, guess what? How is it that these homes are not able to adapt to those new owners? And this is something that we at BONE Structure have been able to do because of our integrated design services being able to fulfill so either with outside architects or within our own professional architects inside because of the basic design of our industrial building system platform, we are able just like the human species, we are able to create 8,000,000,000 different propositions that can be come alive with architecture, with personality and character, with local materials so that we make a significant difference not only in creating beautiful home that live in symbiosis with their environment but also long lasting adaptable homes so that you can remove or add on walls, remove or add on windows, basically reconfigure the whole skeleton. Or should I say the outside shell to adapt to what the skeleton enables you to do so. That's part of what makes us unique, is that we're not just designing homes or having homes designed just to fulfill the needs of the individuals that command us to do it. But we also think fast forward into who else might inherit it because that's becoming the trend or should I say it will be forced onto American society. Because of the cost of owning a home while now like Europeans have been doing for the past century is that you will most probably as a responsible parent look at the possibility of leaving that home to your succession to your kids because they otherwise might not be able to afford a home for that matter.
Prefab Review
That makes sense. Yeah, home prices have certainly gone pricey in a lot of markets. Just to sort of get down to the specifics, so if I'm a consumer and I come to you and I call you to say, "hey, I love the homes I've seen on the site. I'd like to work with you. Do you think you can kind of run me through the process of what that means?" Yeah, to understand, you build the steel frame, you know, are you in this example at least, are you also the architect who hires the local builder? How does all this stuff work?
BONE Structure
It's very simple in the sense that we accompany you to make one of those 1,000 decisions you'll have to make in building your own custom home. Meaning that in the past fifteen years we're not using the language or the vocabulary that has become trendy in you know, local sourcing or life cycle or energy efficiency. This is not what bone structure is all about. So as Michael Frank comes and joins us or asks us to accompany him, we will go with a go left, go right, go left, go right, go straight conversation depending on where you are.
Prefab Review
Yeah, sure.
BONE Structure
And how you want to make things happen, so we accompany you in the process. So let's say for one you say, you know, "my house just burned down in Sonoma and I don't know if I want to rebuild there. I'm really scared, they told us it was a 100 year thing and it's been coming back every year, so I guess I'm 300 years older now and so on and so forth." So obviously we have a better proposition because in terms of fire rebuilds we have the utmost technology to prevent that unfortunate or the result of that circumstance, so we will tell you, "listen, we have an inside architectural service. We can design for you." Well, Michael you say, "yeah, but you know what? I have my friend as an architect, and you know he's been prying me to to get his services and so on and so forth. I Wish that we could use the services." No problem. Let's put him around the table. The thing here is that it's a collaboration. It's getting everybody possible around the table that can make this dream come true. So either we go with your outside architect which then,if you go with us it's very simple, what we'll do is that we'll do a design contract service. Human species wants to go one step forward and one step backward. We don't want to corner a client into a service. So if you're not buying a house from us, you're buying first a professional service of design. We will design it. Then we'll go into an immaterial contract which if you desire to go that way which 95% of people do with us because they entrust us with the service and we help them figure out if BONE Structure is the best proposition for them. Before we start working with them, sometimes we do refer them to other prefab or modular or other traditional builders. We're not shy to do that. We want to make sure that it's not a customer relationship we have. It's a client relationship that we develop. And a client for us is a lifetime experience. It's not a transactional thing. So we sit down with Michael Frank and a convenient partner and we set up and review the wish list from there and we make sense of that wish list and the budget because in this industry whether it's prefab whether it's modular whether it's traditional building, that is the elephant in the room. Budget - does it align with what the market can suffice today and that is are we good to make sure we start with the right interpretation of what these variables are then we get our design team to design it. We're very much into digital design. We've been at it and we've been at the forefront of it for the past twelve years, so when I hear people telling me that, "oh yes, now we've got bim." Well guess what, we've been for at least 9 years now. We've always been on the forefront of making sure that in terms of digital technology we are on the edge. So we designed a home obviously with the implementation in mined with everything that mother nature has to offer with what that lot has to offer and so on and so forth. We present that to the clients and we make as many iterations as we need to. Fortunately, our team is talented. Normally we are able to guide the client to make the right decisions as we go and are able to limit those iterations before they get crazy or we get crazy. So we've learned a lot about that and we're proud to say that we have a very seamless process. So then you have the 3D full version I'll drive you through the home if you want you can put the helmet on and you can visualize your home. You can live it and if you want to buy that version and live with that one, that's okay with me. But we'd prefer you go through and go with the real home. And so then we'll be doing the estimate of what that thermal envelope is going to cost you. That's the pure proprietary system. It's the BONE Structure. It's the thermal envelope. It's the insulation. It's the doors and windows and that's basically what makes us totally different. Before you go into the kitchen counter, think of the conversation or plank floors or whatever outside finishes you want because that is whatever intentions are and you know as we say, everybody has some opinion about home decoration. But that is the most important thing because that is what will make you comfortable. This is where your home becomes a healthy environment, this is where it becomes durable, efficient, adaptable and so on and so forth. And then we go into let's look out there if we have not, have I identified them before which normally we did, we will present you to local builders that we have relationships with. If we don't, we will wit Michael Frank with the potential client look at what the community has to offer as the best builder out there that aligns with the philosophy that the client and BONE Structure have already figured out because a client that comes to BONE Structure has looked at different options and has realized as they were doing their due diligence that they were buying into a premium product. They were buying into what is the best to be offered out there. They know what they're getting into. Because it's simple to understand and it's logical and you know, sometimes one of the remarks we get from our potential clients that have just discovered us is why is it that everybody doesn't build this way? It's so obvious and I always like to say that our best clients are not the ones that know what they want. Because everybody comes in with a wish list. Anyone is and it will not be our best clients. They are the ones that know what they don't want. And you know what, I have yet to come to someone that wants to build a house that hasn't heard stories. Whether that's their own stories that they live through or stories they've heard from elsewhere, the whole project became a nightmare at one point or another. Either because of cost issues which in these days, it's a much more relevant issue and today it's exponential but because of delivery issues, because of sourcing issues, because of labor issues and so on. We're very different at BONE Structure we are still able to control the processes because it is part of it. Integrated design proposition, where the process is at the core of what we do, and that's what some of the big names have tried to do. Coming out from the cell phone industry or this industry, there's a lot of people coming from different trades: trying to bring in the outside processes. Well we've understood over the years and trust me, we've done our hits and misses too. We've done our trials and errors. Well, we've come to realize that the construction industry, the residential construction industry is a local market. I don't care how national your company is, at the end of the day it's a local market and this is where we at BONE Structure have worked with a 182 municipalities and townships so far in the US and in Canada. So we know how to deal with these groups and these municipalities, and our technology is accepted proven and tested and easy to understand because of all of its benefits. So we will choose a local builder with our client with Michael. We'll say, "Michael, this is the builder we would like you to meet. Or we will meet your builder with you and we figure out is this the best proposition." Because at the end of the day, what BONE Structure is really good at, and don't get me wrong, we're not picture perfect, my wife is perfect, but the rest of us are trying very hard, but the end game here is to mitigate the risk and this is what this industry is trying left, right, and center. Everybody's trying to come up with some different options. And from the 20 propositions that you have, and I congratulate you with your prefab podcast and the different interviews you've had with with the industry leaders and they all have good propositions. At the end of the day, everybody's trying to beat nature. They're trying to beat the process out of the human nature. We've looked at it from the human nature and adapted the process to help it out. So it's like the labor shortage in California seven years ago. The national homebuilders association has been, and don't quote me on the seven years, it may be 6 or 7 or 8 we should look at my files, but they said that 27% of builders could not find skilled carpenters. Same review two years ago that was before covid now imagine I should have to check it up, I think it was up to 85% of builders cannot find skilled carpenters. So, it's a major issue out there. This is why it's giving the prefab industry an edge but at the same time, the prefab industry has the same dilemma now they can't find labor to work in their manufacturing plants so they're trying to go industry 4.0 and push the envelope there, but that's capital intensive, as one of the companies you've mentioned. And again, you're trying to beat the process out of human nature. And what we're trying to do is to solve the issues and do it the opposite way. So we present you to the builders we have builders. We make the whole equation. We get the variables out of the equation to make it financially sound and to match your budget and match the timing and the planning that is necessary to realize your project.
Prefab Review
So are you doing the procurement even though obviously you're doing the procurement of the framing stuff and it sounds like the windows, but of the non-shell stuff?
BONE Structure
No, the non-shell stuff is that we will partner up with the builder and the client. But the builder, the local builder, which normally has his local resources and so on and so forth. We feel, and sure we're worthy, don't get me wrong, in a business sense we're leaving a lot of money behind, but we've understood that we need to do what we do best and we need to get the client's objective fulfilled and to do that, the best proposition is to be able to have everyone contribute with what they have in their toolbox. So that local builder has the ins and outs of what he can source and how and when. He's got his buddies and you can get those local materials and and so on and so forth and it's better for the planet, etc, etc. So tested and proven from Whistler, B.C. with enormous snow loads to Sonoma Valley to Hawaii, we've built in the Nordic climates and the eastern parts of Canada. We've realized that to respect some sort of a timeline to build a custom home that has a thousand decisions and idiosyncrasies and everybody has their own version of everything and anything. We monitor it but we give a lot to the local market.
Prefab Review
That makes sense. So in terms of, let's use this Sonoma example because it's fairly flat which is one variable we can take out for the purpose of this example. One of the questions we constantly get from people and I know it's not always the easiest for answers around general cost, let's assume in this example, and by the way it's March 23, 2022, so if there's a a steel shortage tomorrow, more than there already is, you know that's not taken into account, but let's assume that you're building I don't know, a 2,500 square foot or 3,000 square foot house in Sonoma on a flattish piece of land. You know it's to your very high standards but like you know, not insane relative to a normal home you build. What would we be looking at from a cost standpoint and I think a lot of times the way that is helpful to listeners to break this down is sort of like what is the cost of your services from a soft cost and from a hard cost standpoint and then you know whether it's a range or specific costs on the rest of the house.
BONE Structure
Michael, I'm so glad you asked this question. I'm sure that out of the 22 or 25 podcasts you've done, this is the question that people push back on. Let me give you my no-nonsense about that and this is one thing I have looked at the industry in the past and I've always come up with the same conclusion. Here's the question - how much does your car cost per wheel? So whether you have a tesla whether you have a BMW an Audi or whatever, you go into a showroom or if you go on any those of those websites and you go and ask how much does it cost per wheel? It would be an irrelevant comparison to what this industry has imposed as an index of cost which is the dollars per square foot which, if you want my no-nonsense about it and even if you don't want it, it doesn't make any logical sense but hey we've always done it this way. The reason is that if you can just imagine with me here and picture this, you have your beautiful lot. You've got this view of the grape vines and so on and so forth and we design a home and sure enough you want mother nature. You want the whole view. You want the whole spectrum. You want those beautiful openings and windows and so we design an eighteen feet ceiling on this beautiful, what you've described 2,300 or let's say 3,000 square foot home. Okay, but then I could show you something just as nice with a twelve feet ceiling
Prefab Review
Right. A lot less glass.
BONE Structure
Not just less glass. That's 30% less structure. 30% less insulation. So the dollars per square foot do not account for volume entry. It does not account for that. So to prove my point, I will come back to my own frustration when I initiated to build a house 20 years ago. It was already more than that where five builders came back to me with a delta of 72% or 77%. So what I'm telling you is, I would dare you Michael to take one design and get its cost by every prefab company and every traditional builder you can get your hands on. And I will guarantee and I will have put money down on the bet that with the same specs and the same details you will not get 2 prices identical.
Prefab Review
Yeah, I mean mean to be clear we don't usually do this with clients all the time but for what I'm describing for example, let's flip literally. Say you know.
BONE Structure
But I know what your question is. Its give me an indication where your proposition is positioned in the marketplace. So we're definitely a premium product. There's no hiding behind that because you know of the glazing, people come to us because of our architectural design because of our large glazing and so on and so forth. So we're definitely a premium product and in the bay area, I mean right now, you can go Bingo and
Prefab Review
Right, for $500 or $600 a square foot would be probably.
BONE Structure
But then again, BONE Structure technology in its terminal envelope is in the vicinity of 30% of your whole budget. So the big responsibility falls on that 70% of oh geez I saw this new flooring or jeez, I saw this new bathub. It's on that bathub is now only 15 grand versus the nice 5,000 grand bath tub we had planned you see where I'm going. And that's what human nature is all about. So that's what I'm telling you. Where we differ is we accompany as best as we can our clients because it's a long-term relationship not only with them but with our own common baby which is the BONE Structure home they're building. And we know for granted that there's a fair chance that in give or take 70 years from now, that would mean that our clients are in their thirtys and they will have a life expectancy of over one hundred so it's safe to say that 70 years from now there will be new occupants to this home and they will definitely want to change the cosmetics and the opening positions and the inside walls and so on and so forth and for that I must say there's very few if just about no propositions out there. It's definitely very difficult with traditional building and even also a little bit cumbersome with what is defined as pure prefab or modular. So I think that's one of our biggest significant advantages.
Prefab Review
That makes sense.
BONE Structure
And then the price point. Yes, we are a premium product but at least one thing needs to be said and we've heard it from our clients and even the ones that were, "oh, geez that's more expensive," but you know 3, 4, 5 years down the road when we survey them, they will tell you it was worth every penny. Even more so if their neighbors went through a flood or a fire or some other mother nature catastrophe because one example I've had very recently from a client, the whole municipality was flooded. So everybody out there that had some sort of a traditional framing whether it was prefab modular or traditional framing, one common denominator - most of them needless to say, that you've got mildew. You've got something going bad and I don't care what they're trying to sell you to get rid of that, it will not because that's what mother nature has imposed in terms of characteristics to wood. It will just suck up anything. With a BONE Structure, what our clients did, they just tore out the whole basement, they hosed down, literally hosed down and rebuilt. They were up and running in thirty days as their neighbors are still playing with claims with the insurance companies and trying to figure out how to get out of that mess.
Prefab Review
That's great. I had one or two questions about your product before we jump into our fire round. I guess one is that you mentioned cranes whether you need them or don't need them for your product; is that something that's necessary? Just because I honestly in Taho or Marin or you know parts of New York, like one of the places we have clients or people who we have conversations with all the time, have issues with just, "hey, I want to put this modular box here and I can't I can't get it down the road or I can't get the crane down the road." Is that something where there's more flexibility with your product.
BONE Structure
Absolutely, it's one of our biggest and I'm not saying we will not use some sort of a boom truck or something like that if need be, but the whole thinking behind it is that you should be able to assemble a BONE Structure system without out any of those materials or any of those. And one thing you didn't mention which is unfortunate as we're all on the same planet and all the echo and movement is making more impact. It seems to try to make more impact in any form when you need to plant or bring in a crane. It's not only to get it there, it's just that they'll have to cut pretty much everything that's on your land in terms of trees to swing that module in place, with all due respect. We've built, I remember that we've built a house and I don't care if you've got a satellite but we've built a house about two miles into a wooded country area that no one in his own right mind would've thought even existed there because even if you would be able to go through the hunt and try to find it, it is so well camouflaged within the woods because we just about cut only the trees that were needed to get the structure assembled meaning the footprint, everything else we left there. So I don't know of any other technology that could have made that happen per se.
Prefab Review
That's great, and the one other thing that I assume is also an advantage but we sort of counsel people when they're thinking about kind of kits and other systems versus modular, all the time. I assume your homes are probably financeable with kind of normal construction loans versus modular specific ones because the draw schedule is different, right?
BONE Structure
Sure, absolutely. And not only that, you know, depending on the financial institution and so on, we've had some pushbacks like any other modular or prefab company out there in the past. But once we get to talk to them and get them to realize what the product is and the logic and the sequence of it and so on and so forth, very rarely over the years have we hit a hard no. But it's normal. You've got to sit in the chair of that person and in one of those institutions or financial institutions that are basically just filling out a form and they have to click on that yes or no, and they just don't know how to answer it and you help them and guide them and help that client go through that conversation. And like I said, we're very agile at making that happen. And back to your building flexibility, we've done quite a bit of infills.
Prefab Review
Awesome.
BONE Structure
Um, so like I said if you imagine doing an infill in the bay area or in downtown Vancouver or downtown Toronto, it's not only that you cannot get big equipment there, it's just that you don't have room to park the damn equipment there. So it's it's more of bring your pieces this morning and assemble those and this is where we are the champions and in that matter even compared to traditional wood framing because even traditional wood framing will have some sort of an issue because they'll deliver bundles They won't deliver parts. If you see where I'm going.
Prefab Review
And it'll be a longer build process probably. Okay, so this has been awesome to get a bit more of a sense of your company, of your story. If it's okay, I was hoping we try to give everyone a quick fire round and get to kind of general issues with the building process. I guess so we've actually heard this a number of times when we've been helping people in Hawaii, "oh, BONE Sructures has done a couple projects over there." Can you tell me a little bit about building in Hawaii?
BONE Structure
We've done one project there. We did it because it was one of our clients and they were willing to go along and we were willing to go along with them. We're more concentrated and we're very focused on our dedicated markets: California obviously being one, now we're moving into Lake Taho, we're very much into Vermont, we're into New York state, and obviously we're definitely into British Columbia, and Canada, and Ontario, Toronto, and a little bit into the eastern parts in Quebec. But California is one of our biggest markets. This is where we're very dedicated because we're natural for it. We're natural for it whether it's for fire rebuild because of all the advantages we offer that. Whether it's because of energy efficiency, where you know we've been net-zero before they've been talking about net-zero. For us, it's a normal part of energy efficiency. It's not just another checkbox on our our wish list. We are in those markets also because clients like I said, there's more and more clients in California that know what they don't want than what they want. So we don't have to educate a client about energy efficiency and eco-friendly and all of that in California for all the good reasons and I don't have to lecture you on that at the same time. They definitely see the value proposition.
And they don't care how much money you have, a dollar spent into a home you want to make sure you get that value and it's not just about materials. It's to make sure that it's a healthy environment. It's adaptable and so on and so forth. So this is where the whole equation makes it the better proposition.
Prefab Review
Next question. I know I've talked to a few people who I believe are developers who have built with you. We work with work with a lot of developers. Do you talk about how, if at all, that's different from a process standpoint?
BONE Structure
For them, we're always you know, at one point, just to give you a little bit of background and show you how we're always looking for better ways of doing things, we at one point had offered only our products to our channel of selected builders. But at the same time we're shooting ourselves in the foot because we had so much demand and so many builders were basically wanting to come to work with this new technology and so we're very open minded. For the past five years, we've opened up the technology and we've basically aligned our processes to accompany those builders and their teams with the product. But again the product per se, the technology is helping those builders make a better business. What the builders are foreseeing right now is they have dedicated workers with them and sure enough because of covid or because John is now so capable that he bought his own pickup truck and he's now able to have his own clients. So builders, unfortunately the top builders out there, that are making the best homes, have the same labor issue as anyone out there. So with a technology that basically has the process built-in means that they can bring on someone to the team show them that this is a c bar from BONE Structure. Look, it goes here. Clip, clip, clip, you've got a thousand to do this morning Bob, go. And trust me these individuals coming onto our job sites get very excited because at the end of the day at the end of 1, 2, 3, 4 days they see what they've been working with and these immediate results. And they do not have to redo and that is one of the most underlying hidden costs from a builder's spreadsheet is the re-due line. This door was supposed to be here. We've redone it. We spent another 3 hours of carpentry. We had to bring in some more material. Let's remove this. Let's put this back. Because of the human nature of the clients, because of the human nature of the laborers, because people don't look at or read plans. That's human nature. So again, because of our integrated technology, integrated design into our technology, builders are facing labor shortages and with a technology like ours they do not need specific taining. They only need to line up holes with a bar and clip it. Even the logic about all of our hardware. We almost have only one screw available for the whole system. Not one, but almost 90% of the screws on that job site is the same screw. I dare you to go on a traditional job site and you'll see that you'll trip over boxes of different screws, different attachments, caulking tubes, and so on and so forth. The same goes with some other technology out there. So we're here again. We've turned the process around from human nature to technology. Not the technology imposing on human nature. As you are one of the consultants out there, I urge you to open up and broadcast that a BONE Structure is open to business with builders. Let's bring in their clients. Let's bring in their resources and let's let us help them give them the bones so they can do what they very do best: do the finishes and so on and so forth. Because the dilemma they have is that with a traditional construction, and you know this, they are as good as their last project. This new project is a totally new prototype for them, in traditional construction, every single home, even if it's a replicate becomes a new prototype with all its hidden costs and myths and hits and misses and labor shortages and not to say materials because I mean quality of the materials we're receiving in terms of the wood industry right now, man I wouldn't want to be there. I wouldn't want to be there. I mean I was talking to a builder who told me that the last job 40% of the structural wood he received be had to turn back which that's just diffifult. So it's all about predictability and where we help out the builders is to help them have their timelines more predictable and that is the biggest variable in the dollar equation right now. For a client or for an architect or for a builder or for a consultant like yourself is that no one has the crystal ball right now to fix a cost because of unpredictability on every front. We at BONE Structure mitigate the risk because we have a predictable system that enables us to assemble and then fill up with the cosmetics. Architecture design into a design and finishes and so on and so forth with what's available in a local market.
Prefab Review
That's great Mark. Thank you so much for being willing to join us today. It's been really great learning about your journey and learning about BONE Structure for everyone listening, if you'd like to learn more you can visit BONE Structure at bonestructure.ca and to learn more.
BONE Structure
That's capital BONE capital s for Structure BONEstructure.ca and I thank you Michael and I look forward to meeting you in person. Because you do have 206 bones and we someday will come back to shake hands. I guess someday, somehow and that will be fun. Yeah this version of covid you know.
Prefab Review
Yeah, it would be great. Yeah, as as we start to come out of Covid seems like is happening. Alright, thanks again. Mark this was great talking to you and we'll hopefully talk again soon. Thanks
BONE Structure
Thanks
Get Our Guide to Buying a Prefab House
Learn how to buy land, select the best house plan, get financing, calculate investment ROI, and more. Save hundreds of hours of research.
We respect your privacy.
Thank you! The guide will be emailed to you soon.
If you want even more support with your project, then signup for Prefab Concierge - our free service where you are paired with a member of our staff who provides you 1:1 support with your potential project -> Learn More
39 episodes
All episodes
×Welcome to Player FM!
Player FM is scanning the web for high-quality podcasts for you to enjoy right now. It's the best podcast app and works on Android, iPhone, and the web. Signup to sync subscriptions across devices.